Jet Thrusters
v Info from Wikipedia v
A jet engine is any engine that accelerates and discharges a fast moving jet of fluid to generate thrust in accordance with Newton’s third law of motion. This broad definition of jet engines includes turbojets, turbofans, turboprops, rockets and ramjets, but in common usage, the term generally refers to a gas turbine used to produce a jet of high speed exhaust gases for propulsive purposes.
A turbojet engine is a type of internal combustion engine often used to propel aircraft. Air is drawn into the rotating compressor via the intake and is compressed to a higher pressure before entering the combustion chamber. Fuel is mixed with the compressed air and ignited by flame in the eddy of a flame holder. This combustion process, significantly raises the temperature of the gas. Hot combustion products leaving the combustor expand through the turbine, where power is extracted to drive the compressor. Although this expansion process reduces both the gas temperature and pressure at exit from the turbine, both parameters are usually still well above ambient conditions.
The gas stream exiting the turbine expands to ambient pressure via the propelling nozzle, producing a high velocity jet in the exhaust plume. If the jet velocity exceeds the aircraft flight velocity, there is a net forward thrust upon the airframe.
Under normal circumstances, the pumping action of the compressor prevents any backflow, thus facilitating the continuous flow process of the engine. Indeed, the entire process is similar to a four-stroke cycle, but with induction, compression, ignition, expansion and exhaust taking place simultaneously. The efficiency of a jet engine is strongly dependent upon the Overall Pressure Ratio (Combustor Entry Pressure/Intake Delivery Pressure) and the Turbine Inlet Temperature of the cycle.
It is also perhaps instructive to compare turbojet engines with propeller engines. Turbojet engines take a relatively small mass of air and accelerate it by a large amount, whereas a propeller takes a large mass of air and accelerates it by a small amount. The high-speed exhaust of a jet engine makes it efficient at high speeds (especially supersonic speeds) and high altitudes. On slower aircraft and those required to fly short stages, a gas turbine-powered propeller engine, commonly known as a turboprop, is more common and much more efficient. Very small aircraft generally use conventional piston engines to drive a propeller but small turboprops are getting smaller as engineering technology improves.
The turbojet described above is a single spool design, where a single shaft connects the turbine to the compressor. Higher Overall Pressure Ratio designs often have two concentric shafts, to improve compressor stability during engine throttle movements. The outer (HP) shaft connects the High Pressure (HP) Compressor to the HP turbine. This HP Spool, with the combustor, forms the core or gas generator of the engine. The inner shaft connects the Low Pressure (LP) Compressor to the LP Turbine to create the LP Spool. Both spools are free to operate at their optimum shaft speed.
Most modern jet engines are actually turbofans, where the LP Compressor acts as a fan, supplying supercharged air to not only the engine core, but to a bypass duct. The bypass airflow either passes to a separate Cold Nozzle or mixes with LP Turbine exhaust gases, before expanding through a Mixed Flow Nozzle.
Forty years ago there was little difference between civil and military jet engines, apart from the use of afterburning in some (supersonic) applications.
Civil turbofans, today, have a low specific thrust (net thrust/airflow) to keep jet noise to a minimum and to improve fuel efficiency. Consequently the bypass ratio (bypass flow/core flow) is relatively high (usually much greater than 3.0). Only a single fan stage is required, because a low specific thrust implies a low fan pressure ratio.
Today’s military turbofans, however, have a relatively high specific thrust, to maximize the thrust for a given frontal area, jet noise being of little consequence. Multi-stage fans are normally required to achieve the relatively high fan pressure ratio needed for a high specific thrust. Although high Turbine Inlet Temperatures are frequently employed, the bypass ratio tends to be low (usually significantly less than 2.0).
^ Info from Wikipedia ^
A Homemade Mini Pulse Jet Engine

The valveless pulse jet engine or pulse detonation engine is the most simple type of jet and is therefore popular among hobbyists as a DIY project. it is often referred to as a ‘tuned pipe’ because its operation depends upon making the parts the right size and shape so that it fires, or resonates at the engines natural, fundamental frequency.
This pulse jet is made from modified copper plumbing parts. Due to the materials used it could only be safely operated for a few seconds, but this was enough to demonstrate the principles of operation. The fuel was provided from a cheap blow torch and was injected into the combustion chamber. This chamber also contained a tiny homemade spark plug. The spark rate could be controlled by varying the power to a HV capacitor connected in parallel with the spark plug.
This image show the basic ‘tuned pipe’ without the spark plug and gas supply. Tuning was achieved by altering the length and width of the parts used. This was quite simple as there are wide range of plumbing parts that will easily fit together.
More details on the DIY Devices page
I laughed my head off to pulse jet engines.Rainer your nuts,You guys are as wild as i was at fourteen!Can’t say any more about the guitar effect guidence systems.Eureka!It Works!
i would be very happy if some one would give me a blue print of a mini jet engine so i can stap it to an aircraft im building
Hehe! Be careful I hear the exhaust gas can be quite noxious!
I made a jet engine out of a smelly old dog and some tooth paste

Go to youtube.com and search for:
Turbine engine boost pipe failure. Turbo based turbine.
this is just a feeling for you guys to see how dangerous this really is.
power stering pump push like 1200psi you have to modify it for the use of cooling a gasturbine
to psyche:
look buddy, your fans are going to catch on fire, (if there plastic) hey but dont stop trying ! the thing your going for it compressed air- first induction,bring air into your tube-next compresion, sqeeze that air down so it is consentrated – next ignition, light that commpressed air on fire with fuel- expantion, that compressed air will expand and grow larger! makeing it look for a place to go- then exhaust, the big finish were you make all that expanding air go somewere usefull. e-mail me for further help at mark_whitaker@hotmail.com BE SAFE !!!
my e-mail is mark_whitaker@hotmail.com, i am intrested in speaking to someone about makeing a very small jet, about 5 inches long, i have 5 diffrent plans but not the tools to make them.i just want to know if yall think if it will work or not. thanx- e-mail me !
i built a pulse jet but it does not seem to work. I think the problem might be located in the intake, because the way it sounds now is not high frequency pulses but more like a harley davison on idle only slighly higher. The intake of my jet is only 0.5 cm bigger than the tail pipe but will reducing the length of the intake pipe solve the problem? thanks for any help given.
hey im only 13 but im building a cheaper jet engine made out of computer fans and i was woundering if the food catcher in your sink (the thing with holes for water bet stops food) would work for a flame catcher.Also im wondering why no one just buys a gas grill and uses the ignition and fuel injectors from a grill????? thanks 😀
New engine works great. preforms just like a rc turbine engine, no smoke or overheating, the video is on youtube.
This is my new engine after the 2 that exploded. this one will run on veggie oil and water injection.
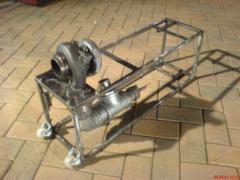
what kind of fuel do you guys use? email me at feedeewannabe@hotmail.com
The turbocharger blew up.
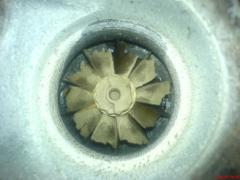
The engine works, but it failed because one of the pipes blew up because of to much heat in the c-chamber. the turbo leaks oil.
wy not mack a tv sho
What is the max speed of the turbine tip? My calculations says +- 1600 KPH. Which means that the max RPM on my turbine is 142 000 RPM with a blade diameter of 60 mm. I don’t want to kill myself someone help me.
My oil pump: 11 bar , +- 25 GPM, with a 12 v drill engine and a power steering pump. it broke my oil pressure gage.
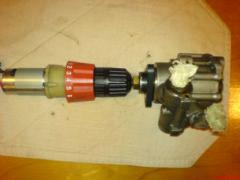
Completed rig without combustion chamber and turbine. soooo saxy!!!
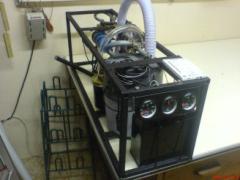
almost completed rig.
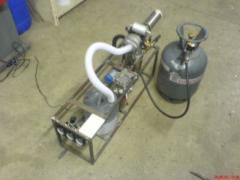
I have an old car that might be useful for a valveless pulse jet.What kind of parts should i take off the car for the pulse jet engine?
this image is resized to hide the working principle of the new engine.
I have witnessed a brand new principle for a petrol powered engine, I have seen and heard the first and only engine of this kind in the world. THIS IS HISTORY!!!
this image is resized to hide the working principle of the new engine.
I an kind of scared to show how it works, because it’s top secret and the only reason that I saw the engine was pure luck. right place at the right time.
Any body that is interested plz e-mail me @ rainerfilm@gmail.com
Don’t expect to see any images, I am planning on selling them on e bay.

Can someone plz help me with a 12 volt 60 psi oil pump. my e mail: rainerfilm@gmail.com
This is my control panel, the speed will be adjusted with the gas regulator pressure. the 3 gages is a temp gage for the oil, a amp meter and a oil pressure gage. The 6 switches will be used for MAIN, oil pump, cooler and starter, ignition and fuel pump.
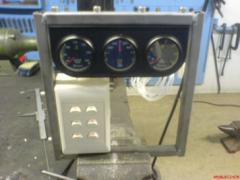
Note that the C-chamber sits in the compressor side.
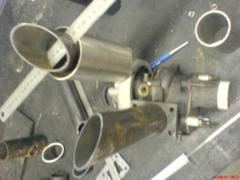
This is going to be a seriously hot pipe.
This is my design for my new C-chamber, this time it sits on the compressor side. The green aria is where the combustion will take place, this means that the fuel has more time to burn by combusting thou the pipe.
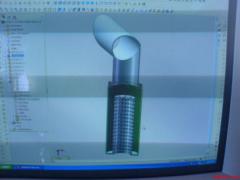
this is my new rig lay out, this one has a after burner.
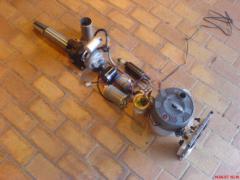
SUCCESS!!!! My turbine works. I an busy re building the turbine engine into a much smaller rig or box, The only problem that I have is to find a 12v oil pump. the cooling system for my new rig is used for 3 things, cooling the oil, cooling the turbocharger, and starting the engine, note the oil tank.
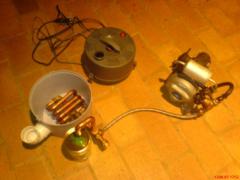
You can see several pictures of fire and plasma on the plasma page. Not seen anything on an actual jet engine though.
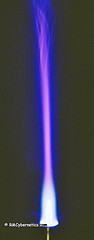
hey guy’s looks like you got lots of cool stuff going on on this site, but hey I have some crazy ideas and wondering if there has been any thing invented yet for an add on to a terbine engine to increase the thrust or make turbine engines possable for space travel.. my basic theroy is proving the action and reaction effect, with an electrical manipulation and corect catalyst. It would basicly be combinding the the bifeild brown effect with todays tech and fuels
lol and a whole bunch of other stuff..;) hey rmcybernetics, jlnlabs great job on your stuff!!
would be great to see a coment on this.
i would like to know if i could start a mini ramjet engine woth a ducted fan
I’ve come up with a F*&^ing good idea to get rid of the co-axial combustion chamber, in a ‘turbo charger’ turbine. I’m going to attempt a common rail injector set, and a set of stators, in the chamber, in the space that’s wasted, between the intake, and exhaust. I have the right people to do the welding…, etc. I’d really like a hand with the technical stuff, if anyone’s interested, though. I can be reached at marty.smith181@bigpond.com , if anyone’s interested in giving a hand. We could end up with a really intetresting design, at some point.
I would like to find out about turbo jet engines made with turbos from SEMITRACTOR TRAILER TURBOS
i would like to know the in’s the outs whatever you can share with me. I have just finished my shop in my garage and am now ready to start production on my propulsion hobby that has always interested me if you have any insight on this subject please feel free to e-mail me at CRISTO.ALLIANCE@GMAIL.COM
hey built a coil gun if you want to see go to http://www.justinlaird.piczo.com
i have a pulse jet but im not sure if it will work or not it sound like a harley davison with out a muffeler a splttery sound but not quite a buzz it is small and its so loud when attempting to start it the neighbours get angry i havent got a start yet but want to know if it will based on the following desriptions
looking for jet terbine type engine plan with material or metals i tried but the tech was not so good if you have any send at mintukalsi28@yahoo.com wating for reply thanks
An internal spark plug can make ignition easyer. The size of the spark plug should be insignificant relative to the size of your jet, otherwise the total volume inside will be reduced. This would increase the resonant frequency of the jet.
ive made a valveless pulse jet but have problems with starting techniques.
should i introduce a spark plug to help?
im a little worried that the spark plug will change the diamentions of the jet and reduce its frequency.
You young guys (12-16?!) are crazy and bright!
Please do be careful when working with these things so that you can grow up and continue to build ever more complex and impressive stuff. You are very fortunate to grow up with the Internet, let me tell you! Follow your curiousity and some day you’ll be rich, or at least happy… Always keep a fire extinquisher near by!
Peace,
Old geek guy
im sorry my email for me is cristo.alliance@gmail.com
I HAVE BEEN TRYING TO FIND OUT SOME PLANS TO BUILD WHAT IS SAID TO BE IMPOSSIBLE A JET ENGINE FROM VACCUM PARTS IF ANYONE HAS ANY INSIGHT ON THIS SUBJECT OR HAS STARTED IN BUILDING ONE BUT HAS HIT A DEAD END PLEASE E-MAIL ME WHAT U HAVE FOUND SO MAYBE WE CAN FIGURE IT OUT I BELIEVE IT IS POSSIBLE I’M JUST NOT SURE WHERE TO GO TO FIND OUT MORE ABOUT THIS MATTER PLEASE IF ANYONE HAS ANY INFO ON THIS EMAIL CHRIS.ALLIANCE@GMAIL.COM
I am looking for a new or good used turbo jet
of the type made by MicroJet I would like to get an FXR 100 which weighs about 10 lbs and generates 95 lbs of static thrust. i plan to try using oxygen enriched fuel.
I want to take this engine to high altitude.
I would be interested in any info related to aquiring one of these engines(the factory has not responded to my quries.
looking for info. I will describe my project if you reply.
Willie
My e-mail is willlielinn@yahoo.com
thanks
Maybe a MagnetoPlasmaDynamic Thruster would intrest you. It’s not really something you can just knock up at home from some plans on the web though. Just Google magnetoplasmadynamic propulsion
i you know how can you send plans for a plasma rocket engine or even build one to show on the site
Geoff, BillyD, Thanks for your comments. Saftey 1st should go without saying really. There’s warnings on the projects, DIY Devices, and Experiments pages. There are also a few warnings in the comments of some of the more potentially dangerous projects.
As for the jet powered bike.. I think there are many enthusiastic individuals eager to make something cool to show their friends. Most people underestimate the the complexity of the project or the level of commitment requried. Fortunatley these people are unlikley to ever produce any sort of working jet powered vehicle.
This obviousley doesn’t mean that they wont hurt them selves while trying. The best I can do is provide good information, and this medium for allowing the exchange of ideas and information.
There are also no step by step instructions so people can’t just try to replicate a project. It is important that anyone making these sorts of projects should know enough about the subject so they can complete it safley.
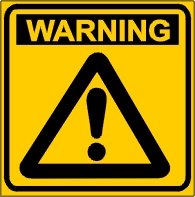
I’d like to encourage you guys to continue your experements in as safe a manner as possible. You are obviously bright guys. So, I believe that you are all smart enough to limit the amount of danger that you expose yourselves to during your experementation.If not,we’ll have to find out the hard way! It may sound cliche’ but safety firs.good luck!
Anyone who is thinking about building this wonderful device should understand three things:
1. Its dangerous!
2. Its dangerous!
And,
3. Its dangerous!
Now I know that technically that’s only one thing, but I thought it was such a BIG one, I’d mention it three times! One slip and you could be scarred for life, or worse! If you’re a knowledgeable adult and you’re careful, it’s a big risk, but so are many things. If your a thirteen year old who wants to build a pulse jet skate board, DONT DO IT; IT WOULD BE THE MOST DANGEROUS VEHICAL ON EARTH!!! I think this site is one of the most interesting and brillant sites on the web, with some of the most interesting projects, but its importain to do a lot of background reading before messing with high force/temp devices.
well if it dosent work i now know where the problem is
yes but what about the nozzels do they come out enougth for optimum frequency or are they to flat faced
I’ve drawn around what I think is a cross section of your combustion chamber. I don’t know if the shape you have is ok or not, but if you compare your design to other jet engine plans, you might be able to get an idea. Look at the dimensions and think about the relative volumes of gas in each section.
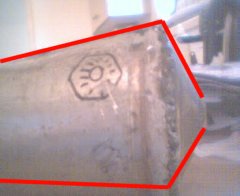
I can’t say much more realy. Small bubbles should be fine, but if they are going to obstruct airflow, or introduce significant turbulence into the moving air, then I would consider grinding them down with a dremel or equivalent tool.
thanx and what about the nozzles by the way the bubles are internal meaning the inside
I can’t quite tell what i’m seeing in that picture.
I don’t know how much the bubbles would effect the operation of it. If they are only small then I guess it shouldn’t be a problem. Just look at it as a musical instrument. If you think it would stop it playing properly then it is probably going to effect performance.
this my jet progress. i have bubbles in my weld bubles in my chamber will this effect it. also dose my nozzels look far out enougth for the frequency.
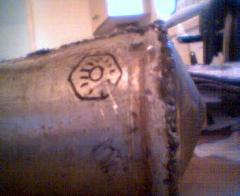
I am planning to build a turbine engine with a Turbine Wheel Shaft from a truck; I will build the combustion chamber around the two wheels
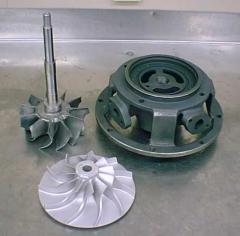
its ok i fixed it
this is my biggining of a pulse jet but was wondering dose an oval shape combustion chameber effect the overall result.
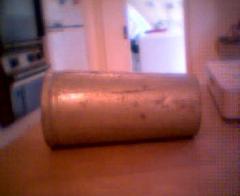
this is my biggining of a pulse jet but was wondering dose an oval shape combustion chameber effect the overall result.
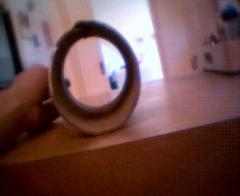
Rainer:
I’m not sure about using glue and plastic pipes for your jet. The metal will get very hot when active which will probably melt the glue and the palstic.
I don’t know what dimensions your parts must be, maybe you could compare with some plans or another project like this homemade turbojet.
coffey:
Sorry, I don’t know. Never used a car turbo or oil system before. Maybe the link above will help.
im making a turbo jet but need some background inforation first. would a turbos oil system work with only a car fuel pump to power the flow?
What size must i make the exaust nozzle? the diameter is 45 mm
I am building a turbine engine out of an old diesel turbo. So far so good, I haven’t started it jet, because I do not now if the PVC pipes used to connect the compressor and the combustion chaimber can handle the pressure. I used an extremely strong glue to connect the pipes. Can someone e-mail me an answer plz? And it is heavy (15 kg), will it be able to move it selves? And can the turbo be damaged if it lay around for two years (filled with oil)? rainerfilm@gmail.com 19jrs old.
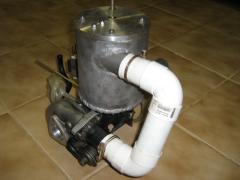
hers pictures of the jet running its last time
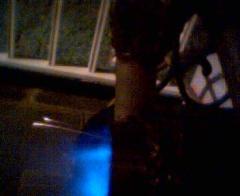
hey justing could you email me some plans on how you made the jet engine with only a vaccum motor Kendallhamrick@gmail.com thanks
Justin, the majority of combustion does not actually happen in the combustion chamber, but rather in the tailpipes. It is important the when the fuel is detonated in the chamber the flame must be able expand into the tail pipes. If the long exauhst is too thin then too much will be forced out of the other pipe which means that hot gasses are not sucked back in to detonate the fuel again. It is the hot gas in the long pipe that re ignites the fuel.
The short pipe provides most of the thrust and also is where most of the the fresh air is sucked back in.
The inrushing air collides with the fuel and hot gasses from the tail pipe which then detonate again. With smaller jets like these is can be difficult to get the amount of fuel/air correct.
Your tailpipe must also be long enough to contain the pressure waves. If it is a bit too long then your jet should still run, but if too short then it wont be able to self sustain the fuel ignition.
MY THERORY
The combustion chameber is the most important as it provides power to the tail pipe and the vaccum. the other pipes are adjustable. the pipes have to arranged in such a way that the sonic wave length can become posible in the chamber.
which one the inlet or the tail pipe?
whitch pipe should be increased?
the inlet i have is 23mm and the tail pipe is 20mm and they fit in each other.
Yes they are very simple in theory as it just a ‘tuned pipe’ with the right bends and diameters, but they can be difficult to make if you have limited availability of materials, pipe sizes etc.
Where practical it is often useful to make many parts of a project adjustable or interchangable so that you can learn how each adjustment will effect the overall performance.
If you increase the diameter of a pipe, try to use a pipe the will allow a smaller one to fit inside. This allows you to easily change the inner diameter of the pipe. You can see an example of this on the DIY page where the top image shows the opening nearest the combustion chamber. There is a n extra bit of pipe inserted just to narrow that part a little.
If your jet is only firing when you are blowing the start air into it, then you would possibly need to increase the diameter of a pipe.
should i make the intake bigger to provide more oxygen and compression. you know for the easyest or simplest jet its hard to get right.
I think the combustion chamber might too large relative to the diameter of the pipes.
After the fist fuel detonation a vacuum remains inside which draws in fresh air/oxygen and also some of the flame in the exauhst to start the next detonation.
If the chamber is too large (or pipes are too narrow)not enough air will get back in time for the next pulse.
I can’t see the end of it on your picture, but maybe the longer pipe shoud taper outwards a little. You could also try a more volatile fuel mix. Adding a few drops of lighter fluid into the combustion chamber can allow you to have a stronger detonation for at least a few pulses. Once it is warm it evaporates and mixes with your gas to give a boost in power but it won’t last long. Make sure you don’t add too much though as you don’t want it firing burning liquid out of the exahusts.
this is another project of mine.
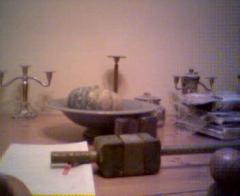
you know that feel you were talking about this was as close as i could come for the tubes i have.
dose it look right?the inlet 20mm tail pipe 23mm and the combustion chameber 70mm.
dont worry about the cracks i havent welded it yet.
It’s hard to say for sure as I don’t know of any designs using square tubing.
I suppose theoretically it would be best to use smooth curves as this will reduce internal drag and turbulence inside the engine. I am unable to say if square tubing is enough to prevent a jet from running correctly but it probably doesn’t help.
dose square tubing effect the overall result of the pulse jet at all?
Nope, not actually Stan, but a fan. You guys who are 12-16 are on the right track. Take the passion into the hydrogen on demand sector. Just be sure to be safe in whatever area you’re in. I don’t think I’d want to be the car behind a jet propelled car, don’t think you’d want to be either.
In any case, you could power your jets on hydrogen derived from water. If you have any electronics experience, make a high voltage, low amp square wave (pulse) controller unit with a frequency of 42.8 khz. Search the web, there are over-unity sites with info.
Search for “peswiki video” or “pesn” for more info. Also, search for “runs on water” videos on youtube or google video. That’s one place to get started.
Free energy should always be free… like freeware should be free or freedom should be free, with no strings attached. We must be responsible with our freedom and free energy. It’s our duty.
If anyone comes up with a jetpack idea that runs on Hydrogen, keep it under wraps until you’re ready to actually test it. Make sure it passes all safety codes and make us all proud.
🙂
the real great thing about this is that this could acctually replace car engines completetly. think about it, you could run three of these in back of your car, using propane or even corn oil, cleaner, less burn with the same or more power. also, much cheaper to fix. i have seen this on other various sites, nothing new, but surprisingly inovative. engineere guy who noticed every one is 13 or 14, we should bump heads on this topic to see what we could accomplish with this type of info and knowlage. seriously, this could be an enormous change furturisticly in the transportation development and enginering. we could make an underground project, or club, of cars, toys, ect. of instruments of trnsportation that soaly move by these turbine devices and perfect them.
Is just me or does everyone on this site claim to be 13 or 14…you all should really be learning why such devices work (the mathematics behind it) rather than build something you know essentially nothing about. Its great that the interest is there, but know why and how it works is more important than having a maching the works & not knowing how it works.
P.S. I’m a Mechanical Engineering student finishing my undergrad degree on related topics.
Type your message here sup? im 13,and built many dangerous things including potato guns, bombs, alcohol stills and i hop up briggs engines 4 fun.a jet powerd sk8board is next
Hi justin just wondering when you got into engines and if you have any plans to build biggers ones or ones that can fly r/c planes probaly gas turbine ones email me at jameskilroe@gmail.com
Thanxs James
P>S I am also just 15
who said you can make a jet from a vacuum? Mythbusters. Heres something to prove them rong.
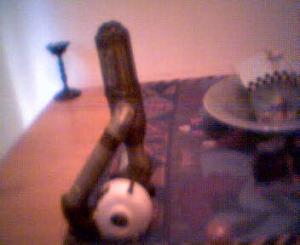
Rember im only 15-16 years old. This jet works to we that is to say me and my friend tested it.
As it picked up speed the fuel run out.
Thanks Justin,
The fuel inlet is just a brass pipe like the ones you find in a hobby shop, soldered into position.
The rest of the jet is made from standard copper plumbing adaptors. The combustion chamber is the only modified part. It is made from two adaptors that are used to connect a small diameter pipe to a larger one. These are cut shorter and soldered end to end. The main drawback of this is that the solder will melt and the device will fail (or even explode) after a short time.
how do you make the nozzels for the combustion chameber?
p.s best site yet